當火花塞散亂堆疊、金屬管件反光干擾、汽配件姿態(tài)無序——傳統(tǒng)機械臂陷入“盲抓”困境時,富唯智能的3D視覺引導(dǎo)機器人進行抓取系統(tǒng),正以99%的抓取成功率顛覆生產(chǎn)邏輯。
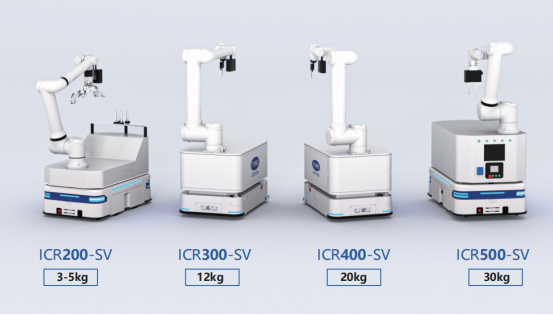
在汽車零部件工廠的料框中,數(shù)百個火花塞無序堆疊,環(huán)境光線從晨到暮劇烈變化。工人肉眼分揀效率低下,機械臂因無法精準定位頻繁漏抓——這正是富唯智能切入的戰(zhàn)場。通過AI+3D視覺+機器人的深度融合,我們讓機械臂真正“看懂”世界,實現(xiàn)毫米級無序抓取革命。
一、攻克工業(yè)抓取三大“死穴”,柔性智造破局而生
無序來料、光線波動、多品類混線——傳統(tǒng)自動化方案難以逾越的障礙,恰是富唯技術(shù)的核心突破點:
1.深度學習穿透視覺干擾:自研AI算法融合3D點云與RGB數(shù)據(jù),在廠房入口強逆光、金屬反光等場景下,仍可實現(xiàn)±0.2mm的定位精度,徹底解決光線變化導(dǎo)致的識別失效問題;
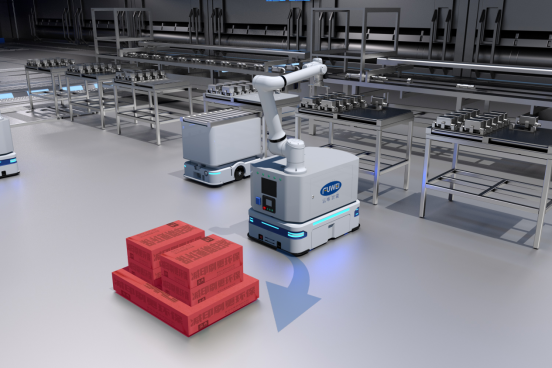
2.動態(tài)避障規(guī)劃智能路徑:機械臂結(jié)合碰撞檢測算法,在0.5秒內(nèi)生成最優(yōu)抓取軌跡,即使料框中工件交叉堆疊,也能精準避讓障礙完成抓取;
3.多品類零切換適配:同一系統(tǒng)可同時識別螺釘、金屬管、汽配件等不同工件,通過模塊化功能庫即時切換任務(wù),攻克“小批量多品種”生產(chǎn)痛點。
二、三大技術(shù)引擎,驅(qū)動抓取效能躍升
富唯智能視覺引導(dǎo)機器人進行抓取系統(tǒng),以硬核技術(shù)重構(gòu)效率標準:
1. 自研高精度3D視覺定位引擎
采用激光結(jié)構(gòu)光與雙目成像技術(shù),對反光金屬件生成百萬級點云模型,即使面對光滑空心金屬圓管,仍保持99%抓取成功率,放置精度穩(wěn)定控制在0.2mm內(nèi)。
?
2.?全場景柔性適配架構(gòu)
從汽車火花塞分揀到新能源電池模組搬運,系統(tǒng)提供預(yù)置的機器人控制、視覺標定、工件模板庫,新產(chǎn)線部署周期縮短70%。某汽配企業(yè)導(dǎo)入后,替代12名人工,實現(xiàn)180天零故障運行。
?
三、落地價值:成本減半,效能倍增的數(shù)字化轉(zhuǎn)型利器
在金屬加工車間,富唯視覺引導(dǎo)機器人進行抓取系統(tǒng)正創(chuàng)造真實效益:
“來料管件無序堆疊且表面反光,人工每小時僅處理200件,而機器人單工位產(chǎn)能突破600件,精度達標率100%” ——某電機殼體制造商實測報告。
?
富唯智能視覺引導(dǎo)機器人進行抓取技術(shù)已深入汽車、新能源、精密制造等領(lǐng)域。未來,我們將持續(xù)深化視覺感知與運動控制的融合,讓每臺設(shè)備不僅是執(zhí)行終端,更是產(chǎn)線的決策節(jié)點——因為真正的智能制造,始于“看得懂世界”的機器之眼。
當傳統(tǒng)自動化困于剛性邏輯時,富唯以動態(tài)視覺撕開裂口:環(huán)境光劇變中識別金屬反光件,無序堆疊里規(guī)劃最優(yōu)抓取路徑——這雙“慧眼”正在百家工廠晝夜不息地重塑生產(chǎn)邊界。